Escape the Trap of LCDs, Buttons and Keypads
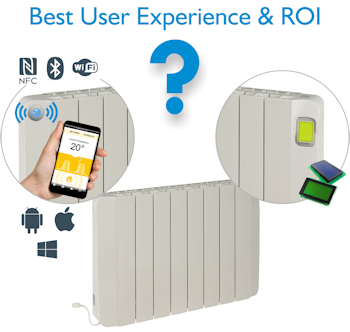
Old-school, on-board HMIs are losing ground to mobile apps.
As soon as electronic equipment requires configuration, it also requires a Human Machine Interface (HMI). The most common solutions are either an LCD display and navigation keys, or a tactile LCD.
Both solutions are frequently used in industrial equipment and consumer appliances. Take for example:
- Electric radiators: European legislation now requires built-in controls for programming hourly usage, which necesitates a moderately complex HMI.
- Welding stations: Professional systems are increasingly accessible to DIY enthusiasts and with increasingly sophisticated configuration controls. Such interfaces are both complex and subject to extreme conditions.
These examples are worlds apart in their use, but very similar in terms of the problem of configuration and HMIs. Increasingly, both systems require programable electronic controls. In some cases those controls will be required by laws or safety standards. Further, in both cases the first instincts of the designers of these systems will be to create an LCD-based HMI.
The question to pose today - Is the creation of an LCD-based HMI really the best approach for the end-user, and for the ROI of the companies designing these systems?
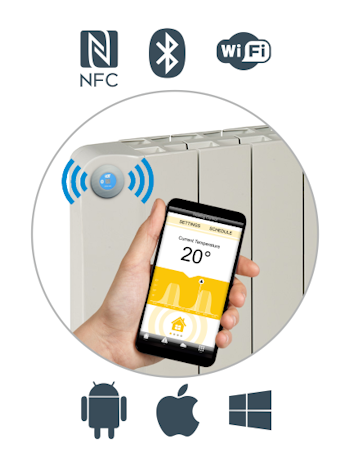
The Duetware solution for mobile HMI apps
Mobile phones present a new alternative to the on-board LCD. They are also an alternative that is much more accessible than one might imagine. Duetware-based products allow designers to elaborate HMI for specific use cases for their electronic systems, then immediately and incrementally create corresponding HMIs on mobile phones. Duetware is the heart of a complete solution that facilitates all aspects of this integration.
First, for connectivity, Duetware-based wireless modules are available for three types of mobile connections:
- NFC for configuration of equipment
- NFC with Bluetooth Low Energy for longer duration connections when configuring or supervising equipment
- NFC with Wi-Fi when a permanent connection to a network is necessary.
All of these modules benefit from NFC for improved ergonomics, security and power consumption. They are all complete wireless designs, include optimized antennas and are certified.
All modules have the same form factor and the same wire interfaces to connect to the target equipment. This simplifies physical integration and improves flexibility for designers. Changing wireless technology with Duetware-based products is as easy as plugging in a new module and configuring it.
These modules are simple to implement. From the IoTize Studio software environment, electronics designers configure the connection to their target equipment, then generate and test their mobile apps. Creating a first HMI app can be done literally in just minutes (video).
By eliminating the challenges and expertise required for wireless integration and app creation, the Duetware solution reduces:
- Overall project complexity
- Design effort and time
- Risks of project failure and dead ends
By doing so, Duetware shortens time-to-market of an initial project and subsequent evolutions. This greatly improves the possibility of capitalizing on opportunities and improves the return on investment.
LCD vs Duetware-based mobile apps
To understand the tradeoffs there are several aspects to consider.
LCD & keypad designs |
Duetware-based mobile apps |
||
Usage |
|||
Ergonomics | HMI logic is specific to a manufacturer and often unclear to users. User manuals required. | Users are familiar with mobiles & apps. Online help can be directly accessible. | |
Physical access | Users have to sit or kneel next to equipment to access the HMI. | Users configure remotely over a wireless connection adapted to their use (range, bandwidth, etc.). | |
Wear | Contacts on keypads age poorly. LCDs are sensitive to abrasion (dust, splinters, dirt). | Wear is managed by users themselves, for whom the mobile is a constant companion. | |
Connectivity | Cloud connectivity must be managed separately from the HMI. | Configurations can be saved to the Cloud via a direct connection (Wi-Fi), or mobile's data connection. | |
Security | None, or weak access control (ex. enter a code). | NFC complements security of Bluetooth and Wi-Fi. | |
HMI Development |
|||
Duration | Long due to management of HMI firmware, hardware and mechanical integration. | In minutes for a PoC because all key aspects of implementation are done. Just connect and configure. | |
Complexity | High due to need for qualified subcontractors, and HMI design study. | Low due to pre-implemented features and mobile app design in intermediate steps. | |
Tooling | Keypads and screens require specific tooling (cost, time). | Little specific tooling. | |
Evolution | Each evolution requires firmware redesign, and new tooling (cost, time). | Done rapidly by updating configuration and apps. | |
Other... |
|||
Cost | High per unit cost due to high development and tooling costs. Prohibitive unless producing in very high volumes. | Low integration and tooling costs yield lower per unit costs. | |
Consumption | Low consumption, except for LCD. | Low to none (NFC). Depends on the wireless technology. |
Mobile HMI apps are the wave of the future
In our first case, the manufacturers of radiators state that only 20% of their customers take the time to program their product because it is so tedious. Thus, the majority of their users don't benefit from the possible control and cost savings that can result.
In the second case, the complexity and difficulty to understand the interplay of welding equipment parameters makes users reticent to modifying them. Users tend to limit themselves to controlling essential parameters, only. In both cases users aren't taking advantage of the functionality that designers are embedding in these projects! Their design investment is wasted.
In both cases, accessing and entering configuration parameters on an app or via website can dramatically improve the user's understanding of the parameters, as well as making it easier to enter changes, or return to an old configuration. Users are more likely to both use and appreciated the functionality that designers are embedding in their products.